Flexible Packaging Burst Testing - ASTM F1140
Packaging Burst Test: Essential Testing for Flexible Package Integrity
In today’s high-performance packaging industry, the packaging burst test is a vital method for ensuring the structural reliability of flexible packaging materials. From food and pharmaceutical products to medical devices and industrial supplies, package failure can lead to product contamination, spoilage, or costly recalls. The burst test evaluates how much internal pressure a package can withstand before rupture, providing key data on seal and material strength. In this article, we explore how this test works, its connection with burst testing of package seal, and how burst seal strength testing supports quality control processes.
Burst Testing of Package Seal: How It Works and Why It Matters
The burst testing of package seal evaluates the package’s ability to resist increasing internal pressure. The process begins by gradually inflating the sealed package with compressed air or gas. This continues until the weakest point—typically the seal or material—gives way. The burst pressure recorded at the moment of failure is critical. It represents the package’s maximum threshold before failure and is used to:
-
Verify seal strength consistency
-
Compare different packaging materials
-
Detect flaws such as incomplete seals or delamination
-
Evaluate new package designs or sealing technologies
Burst seal strength testing isn’t just about seeing when a pouch pops. It’s about establishing safe operating margins for filling, shipping, and storage conditions—especially for sterile or vacuum-sealed products where any breach is unacceptable.
Standards like ASTM F1140 and ASTM F2054 offer guidelines for performing burst strength and creep testing of medical and food packaging, adding credibility and repeatability to the process.
From Burst to Creep: What Happens After Peak Pressure
In many testing programs, packaging burst test results serve as the foundation for additional evaluations. Two advanced methods—creep test na creep-to-failure test—build on this data to assess long-term performance:
-
Mtihani wa Creep: The package is held at a fixed pressure (often 80% of burst value) over a defined period. Any pressure loss or deformation is recorded to assess seal robustness under stress.
-
Creep-to-Failure Test: Here, pressure (typically 90% of burst value) is applied until the package fails. This simulates extreme long-term stress scenarios and helps define worst-case performance limits.
Both methods provide essential insights into how a package behaves under storage, stacking, transport vibration, and real-world thermal fluctuations.
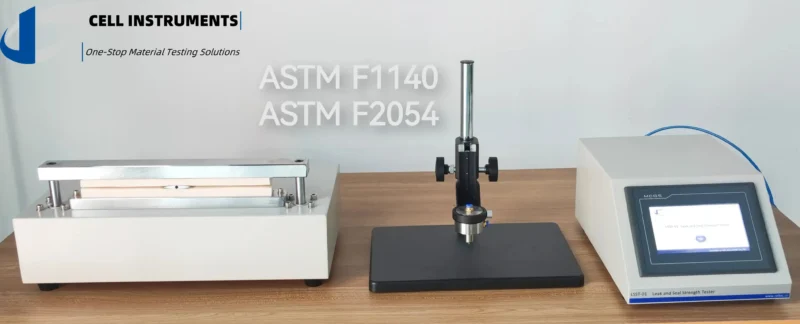
Equipment Spotlight: LSST-01 from Cell Instruments
The LSST-01 Uvujaji na Kijaribu Nguvu ya Muhuri by Vyombo vya Kiini is purpose-built for conducting packaging burst tests, burst seal strength testing, and creep evaluations. It supports a wide test range (0–600 kPa) and accommodates a variety of sample forms such as pouches, bags, tubes, sachets, bottles, and even battery cells.
Key features include:
-
Precision inflation and pressure control using a 0.4–0.7 MPa compressed air supply.
-
Standard and customized jigs for open and closed packaging formats.
-
High-sensitivity probes and ports that ensure accurate pressure monitoring.
-
Test flexibility, allowing both destructive (burst) and non-destructive (creep) testing within one platform.
-
By using a single instrument like the LSST-01, laboratories can ensure consistency across multiple packaging types while complying with global test standards.
When to Use Packaging Burst Test in Quality Control
Manufacturers, converters, and QA teams should integrate packaging burst test protocols at different stages of the production cycle:
-
Design validation: During R&D, when testing new packaging materials or seal profiles.
-
Production sampling: As a part of in-line or batch sampling to check process stability.
-
Shelf-life simulation: When packaging will experience pressure changes during air transport or in vacuum applications.
-
Regulatory compliance: For medical, food, and pharmaceutical packaging, where seal strength validation is mandatory.
Frequent and precise burst testing can help identify issues early, reduce waste, improve sealing machine calibration, and avoid costly market failures.
Conclusion
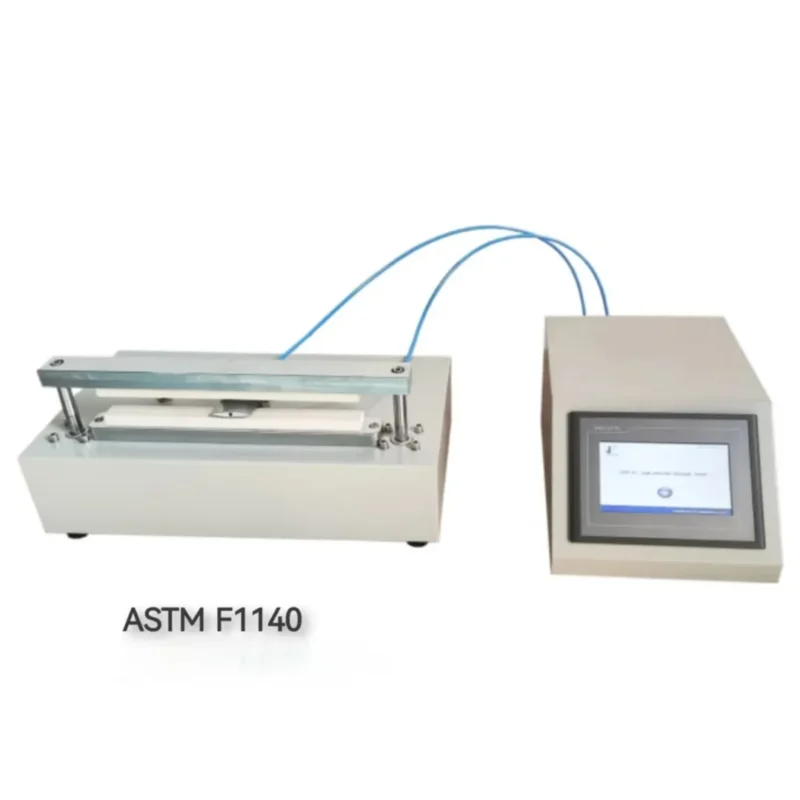
The packaging burst test is more than a mechanical stress test—it’s a critical quality tool that reveals whether packaging will survive real-world pressures. By combining burst testing of package seal, burst seal strength testing, and extended creep evaluations, packaging professionals can verify the strength, consistency, and safety of their products. With advanced instruments like the Cell Instruments LSST-01, companies gain both compliance assurance and performance insights—making burst testing an essential part of modern packaging integrity programs.