ASTM D6653
Test Methods for Determining the Effects of High Altitude on Packaging Systems by Vacuum Method
Ringkesan standar
High-altitude transport can significantly stress packaging systems. Whether you’re in food, pharmaceuticals, or electronics, understanding how packaging behaves under reduced pressure is crucial for preventing product damage. ASTM D6653, Standard Test Methods for Determining the Effects of High Altitude on Packaging Systems by Vacuum Method, provides an effective framework for assessing these risks.
Katrangan standar
ASTM D6653 is specifically designed to simulate the reduced pressure environment experienced during air transport or travel over high mountain passes. Packaging systems may expand, rupture, or leak when exposed to the pressure differential at altitudes as high as 5,791 meters (19,000 feet). This standard enables manufacturers and quality control professionals to evaluate the resilience of packaging under such conditions.
The test is particularly useful in:
- Package design and validation
- Engineering assessments
- Leak integrity testing
- Identifying weak points in packaging systems
Why High Altitude Package Integrity Testing Matters
When products travel in unpressurized aircraft compartments, they experience significant pressure drops. These pressure changes can:
- Deform plastic containers or flexible pouches
- Cause seal failures or ruptures
- Lead to leaks that compromise product safety and shelf life
High altitude package integrity testing using ASTM D6653 ensures packaging can withstand these conditions without failure. It’s a proactive measure, especially for high-value or sensitive goods such as sterile medical devices, food items, or electronics.
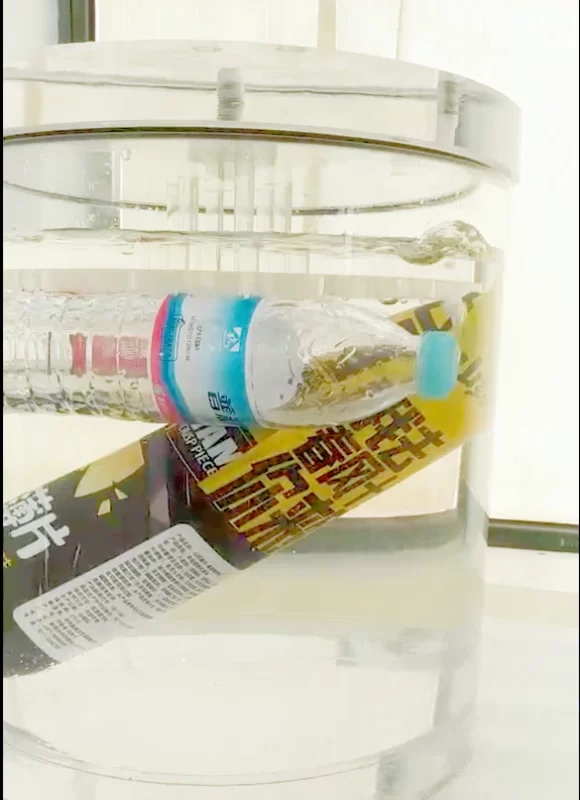
Katrangan rinci babagan Proses Tes
One of the key components of this standard is the vacuum method. Here’s a step-by-step breakdown of how it works:
1. Test Setup and Conditioning
- Specimens must be conditioned at 5.6 ± 2°C for at least 24 hours before testing.
- An alternative standard atmosphere of 23 ± 2°C is acceptable when required.
2. Equipment Requirements
The test requires:
- A vacuum chamber capable of simulating altitude conditions (up to 4,877 m or 16,000 ft)
- A vacuum gauge accurate to within 2%
- Proper sealing valves and pressure control features
3. Testing Procedure
- Place the package inside the chamber.
- Increase the vacuum to simulate altitude at a rate of 305 m (1,000 ft) per 30–60 seconds.
- Maintain the simulated altitude for 60 minutes.
- Slowly return the chamber to atmospheric pressure.
- Remove and inspect the package for any deformation, leakage, or seal failure.
This test does not measure leak size or rate directly but instead provides qualitative results by observing packaging integrity post-exposure.
Vacuum Method Best Practices and Considerations
To ensure accurate and repeatable results when performing ASTM D6653 leak testing, consider the following:
Select representative samples
Use representative samples from production batches
Record all test conditions
Document all test parameters, including altitude simulation level, vacuum duration, and temperature conditions
Benchmark with other standards
Compare results against performance testing methods such as ASTM D4169 for a full evaluation of packaging durability
Ensure controlled, reliable testing
Always perform tests in controlled conditions with reliable instrumentation
Interpreting and Reporting Results
A packaging system is deemed successful if:
- The product remains intact without deformation or leaks
- Seals and closures remain secure
- No internal packaging is displaced or damaged
This data helps stakeholders make informed decisions regarding packaging design, shipping methods, and overall product safety.
Reports should include:
-
Test conditions and deviations
-
Description of the packaging and product
-
Temperature and vacuum parameters
-
Visual observations and failure modes if any
FAQ babagan ASTM D3078
1. What is ASTM D6653 used for?
ASTM D6653 assesses the impact of high-altitude pressure changes on packaging systems using a vacuum method.
2. Why is vacuum method testing important for packaging?
It simulates altitude conditions to evaluate if a package can withstand pressure differentials without leaking or deforming.
3. What industries benefit most from ASTM D6653 testing?
Packaging for pharmaceuticals, electronics, food, and medical devices all benefit due to their sensitivity to air transport conditions.
4. How long should the vacuum be maintained during testing?
Typically, the vacuum is held for 60 minutes, but this can vary depending on product value and shipping conditions.
5. What equipment is recommended for ASTM D6653 testing?
Cell Instruments’ GLT-01 Gross Leak Tester is ideal, offering precision vacuum control and optional pressure decay integration.
Looking for reliable ASTM D6653 leak detection equipment?
Aja kantun kesempatan kanggo ngoptimalake proses kontrol kualitas kanthi peralatan paling canggih.