Bubble Test Packaging- ASTM D3078
Bubble test packaging is a widely accepted technique for evaluating the leak resistance of flexible packaging, especially in industries where product integrity and shelf life are critical. Commonly used in food, pharmaceuticals, medical devices, and consumer goods, this method offers a simple yet effective way to visually detect packaging failures. With packaging standards becoming more stringent, understanding how the leak testing procedure works—especially as defined in ASTM D3078—can help quality assurance teams strengthen their packaging validation processes.
Leak Testing Procedure and ASTM D3078 Guidelines
그만큼 leak testing procedure 에 설명되어 있습니다 ASTM D3078 is officially titled Standard Test Method for Determination of Leaks in Flexible Packaging by Bubble Emission. It uses a vacuum chamber and a liquid medium (typically water) to detect leaks by observing bubble formation. The process involves submerging a test sample in the chamber, applying a vacuum, and monitoring for any streams of bubbles that indicate leakage.
Key steps in the ASTM D3078 leak test include:
- Submerging the flexible package in a transparent vacuum chamber filled two-thirds with water.
- Applying vacuum until the package begins to expand.
- Holding the vacuum for a specified duration (e.g., 30 seconds to 5 minutes).
- Watching for bubble emission from seals, corners, or perforations.
The presence of 거품 방출 confirms the existence of a leak. The test helps determine whether the packaging system can protect its contents against environmental factors such as air, moisture, or bacterial ingress.
This standard is frequently used to qualify new packaging materials or to validate packaging seal processes in high-risk products like sterile medical items or vacuum-packed food.
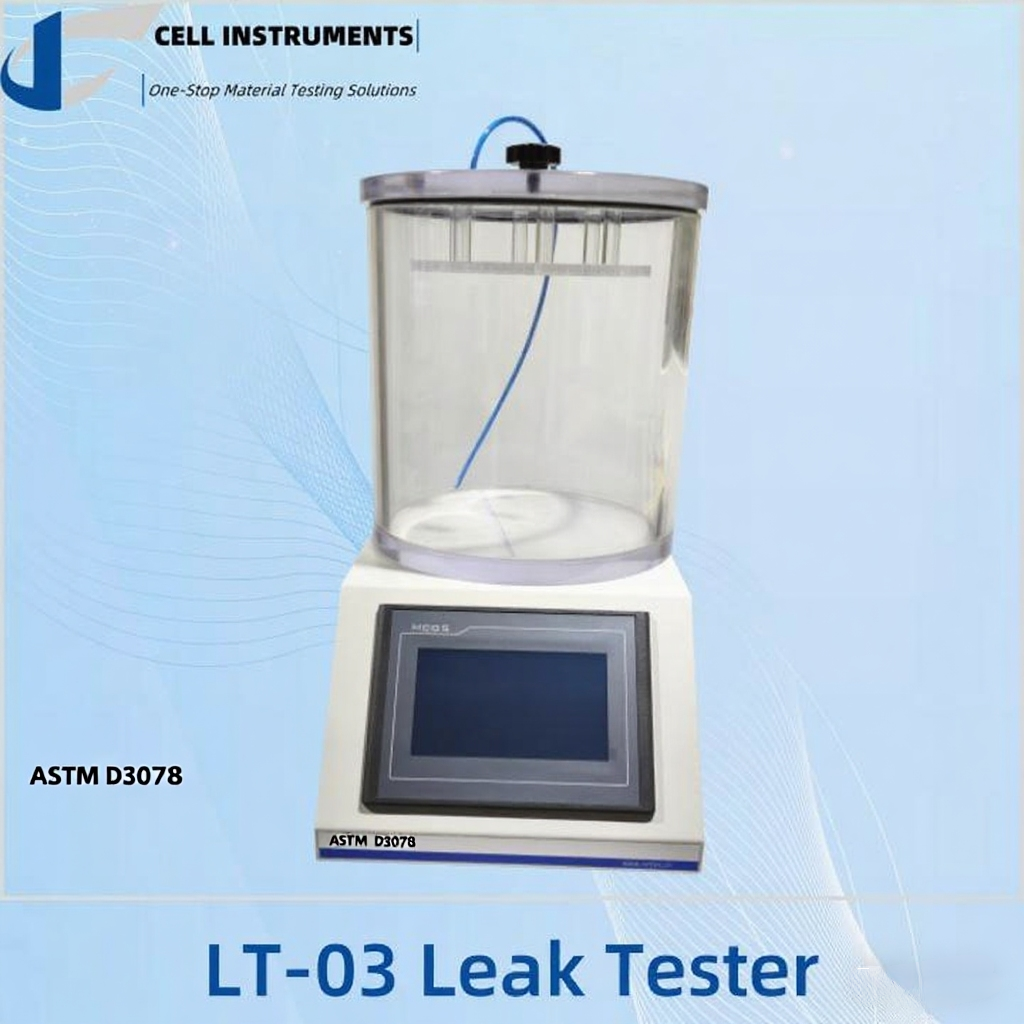
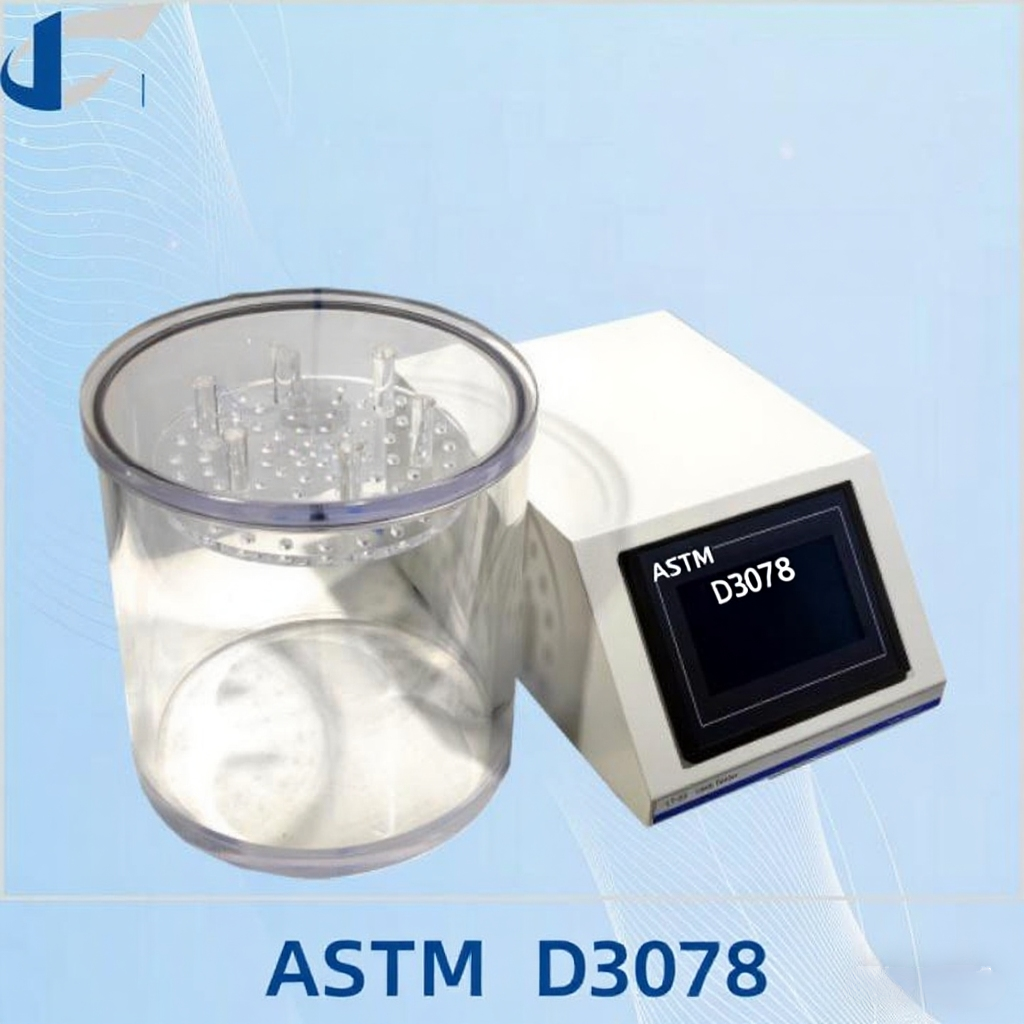
Why Use Bubble Test Packaging in Quality Control?
Bubble test packaging is valued for its simplicity, cost-effectiveness, and clear visual detection. Compared to more technical methods like helium leak detection or vacuum decay, the bubble test offers several advantages for day-to-day production environments:
- Quick visual confirmation of leakage presence.
- Non-destructive to some sample types, depending on vacuum level and packaging material.
- Low equipment investment for labs or production lines.
- High sensitivity to pinhole leaks or seal flaws.
Equipment Overview: Using a Professional Leak Tester
While the bubble test packaging method can be conducted using basic equipment, using a dedicated leak tester—such as the unit from 셀 인스트루먼트—enhances accuracy, repeatability, and safety. A professional leak tester typically includes:
- A transparent vacuum chamber made from durable materials like polycarbonate or tempered glass.
- A precision vacuum gauge for setting and maintaining the desired pressure.
- Inlet and outlet valves to control vacuum draw and release.
- A transparent plate fixture inside the chamber to prevent sample flotation and ensure consistent positioning during testing.
- Digital control interface for setting vacuum level and timing, improving operator consistency.
Reporting and Compliance in Bubble Testing
According to ASTM D3078, a complete leak test report should include:
- Confirmation that the test followed ASTM D3078 or details of any deviations.
- Material and sample identification.
- Vacuum level, fluid type, test duration, and sample expansion observed.
- Clear indication of leak presence, including location if visible.
- Total number of tested samples and number of failures.
- Final statement on whether the packaging passed or failed the acceptance criteria.
This level of detail ensures the test results are reproducible, traceable, and useful in audits, quality validation, or root cause investigations.
결론
Bubble test packaging remains a cornerstone of leak detection in flexible packaging systems. It offers a straightforward, effective method to verify package integrity, guided by the globally recognized ASTM D3078 standard. By implementing this leak testing procedure using reliable equipment like Cell Instruments’ leak tester, companies can enhance product quality, ensure compliance, and protect brand reputation across various industries. Whether used in development, validation, or production line sampling, the bubble test delivers actionable insights into package performance.