Ensuring the safety and sterility of flexible packaging is vital in industries like pharmaceuticals, food, and medical devices. One of the most reliable methods to validate seal strength and airtightness is packaging integrity testing, particularly through the leak testing procedure defined in ASTM D3078. This article explains how to conduct packaging integrity tests effectively, helping quality professionals ensure compliance and prevent product failure.
Understanding Packaging Integrity Testing
Packaging integrity testing evaluates whether a package can maintain its protective barrier under specified conditions. Any compromise in the seal can lead to contamination, reduced shelf life, or non-compliance with regulatory standards. In flexible packaging, air or fluid leakage can indicate critical weaknesses that must be addressed.
Industries such as medical, farmacèutica, i envasos d'aliments rely heavily on integrity testing to meet stringent quality assurance demands. Among various testing standards, ASTM D3078 stands out for its accuracy, simplicity, and applicability to flexible packaging.
Why Follow ASTM D3078 for Packaging Integrity Testing?
ASTM D3078, titled “Standard Test Method for Determination of Leaks in Flexible Packaging by Bubble Emission”, outlines a visual test method for identifying seal leaks. This method uses a vacuum chamber to detect bubble emissions, offering a cost-effective and standardized approach to integrity testing.
Key advantages include:
- Non-destructive for certain packaging types
- Ideal for quality control i comparative evaluation
- High sensitivity depending on vacuum level and packaging material
- Simple setup and observable results
Leak Testing Procedure According to ASTM D3078
To conduct packaging integrity testing in compliance with ASTM D3078, follow this leak testing
procedure:
1. Prepare the Equipment
Use a transparent vacuum chamber equipped with:
- Vacuum-tight lid
- Vacuum gauge
- Inlet/outlet tubes with valves
- Internal transparent plate
- Chamber filled with test fluid (usually water)
2. Conditioning
Ensure both the test specimen and the fluid are at room temperature to avoid condensation or fluid distortion during testing.
3. Sample Selection
Select a representative number of flexible packaging specimens, either empty or filled. The quantity can vary based on product type, cost, and production conditions.
4. Submersion
Submerge the package(s) completely under at least 25 mm (1 inch) of test fluid. Multiple small packages may be tested simultaneously if clearly visible.
5. Apply Vacuum
Close the outlet valve and begin applying vacuum slowly (~1 in. Hg/s) until the desired vacuum level is reached. This vacuum level must be sufficient to detect small leaks without damaging the sample.
6. Observe for Leaks
During vacuum rise and holding phase (usually 30 seconds), watch for a continuous stream of bubbles indicating leakage. Isolated bubbles from trapped air are not considered failures.
7. Evaluate Sample
Release the vacuum and check for fluid ingress inside the package. Any internal fluid or observed bubbles from seal areas confirm a failed sample.
8. Report Results
Document the vacuum level, duration, observations, number of specimens, and number of failures. Identify the test fluid and any abnormalities such as excessive expansion.
Interpreting Test Results
A sample fails if:
- Bubbles consistently emerge during vacuum
- Fluid is found inside the specimen after testing
- The sample expands excessively, reducing vacuum effectiveness
A passar indicates no observable leakage and no internal fluid after the test.
Best Practices and Tips
- Use clean, transparent chambers for optimal visibility
- Always maintain consistent test conditions for comparative results
- Avoid testing packaging with minimal or no headspace
- Document all deviations from standard ASTM D3078 procedures
Recommended Equipment: Cell Instruments Leak Tester
For accurate, repeatable packaging integrity testing, we recommend the Instruments cel·lulars Comprovador de fuites al buit. Our systems are fully compliant with ASTM D3078 and feature precision control of vacuum level, transparent chambers for clear visibility, and customizable fixtures for various packaging formats.
Instruments cel·lulars specializes in materials testing solutions tailored for the farmacèutica, medical, i menjar industries. Our leak testers help ensure your products meet the highest standards of quality and safety.
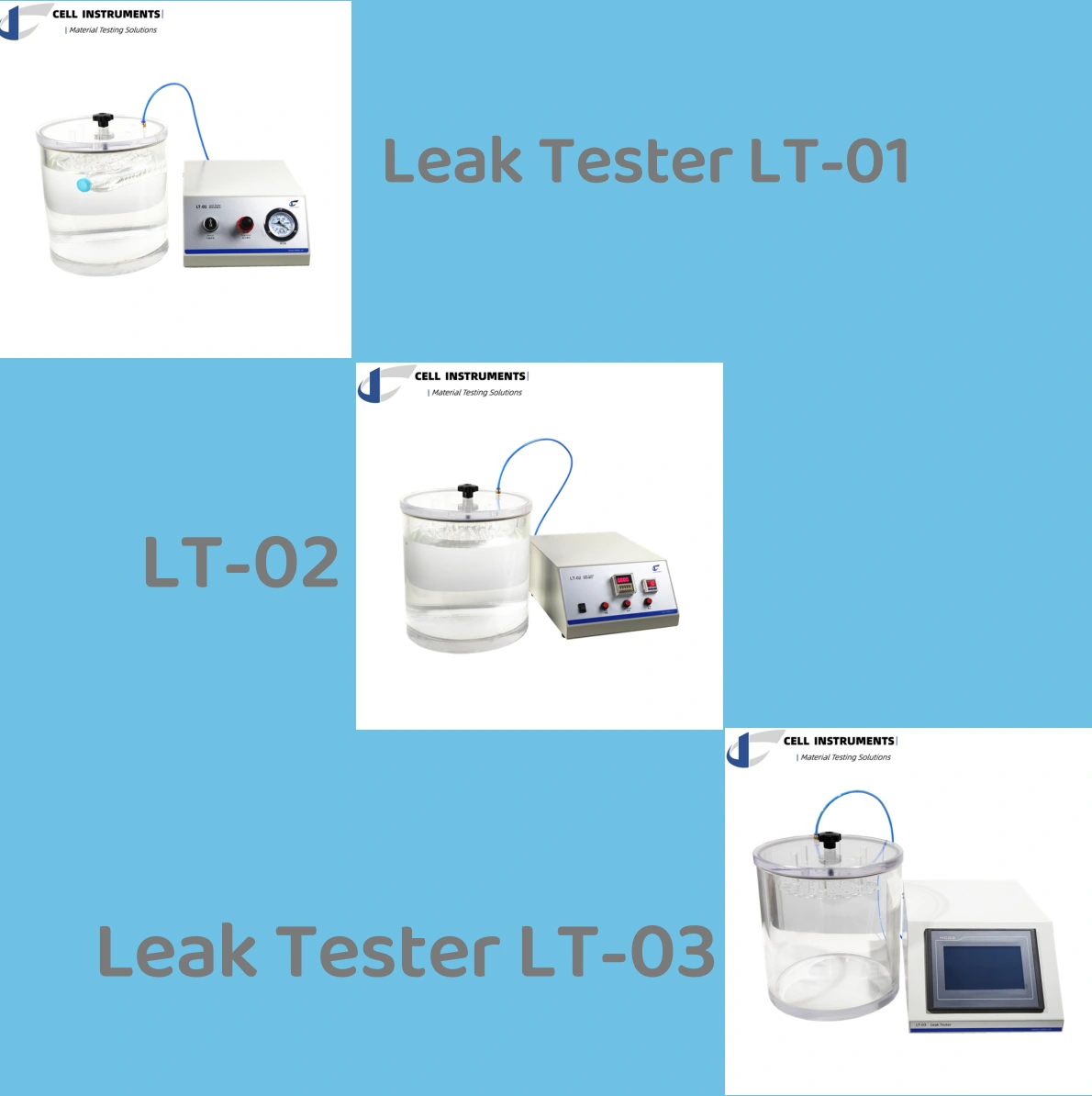
Conclusió
Conducting packaging integrity testing using the ASTM D3078 leak testing procedure ensures that flexible packages maintain their seal strength and protect product contents effectively. By following a standardized, visual-based method, quality professionals can detect potential failures early and take corrective action. For reliable and efficient testing, consider the advanced solutions offered by Cell Instruments.